DARIN COSMETICS LABORATORY, Bangkok, Thailand Cosmetic Cleanroom Engineering Practice: Design and Technology in Tropical Climate
Client company: DARIN COSMETICS LABORATORY (THAILAND) CO., Ltd.
Scope of Business: Soap, Cleaning Compound, and Toilet Preparation Manufacturing, Chemical Manufacturing, Manufacturing, Toilet preparations
Address: 7/11 Phoem Sin Road SAI MAI, BANGKOK, 10220 Thailand
l Engineering background and challenges
During the hot and humid summer months in Bangkok, Thailand (average temperature 32°C, humidity 75%), the design of a cosmetics cleanroom needs to balance the ISO 14644-1 standard (Class 100,000 cleanliness) with the tropical climate. As the core design and product supplier for this project, we focused on modular component development and system integration to provide DARIN COSMETICS LABORATORY with a customized solution that ensures the stability and efficiency of the production environment in extreme climates.
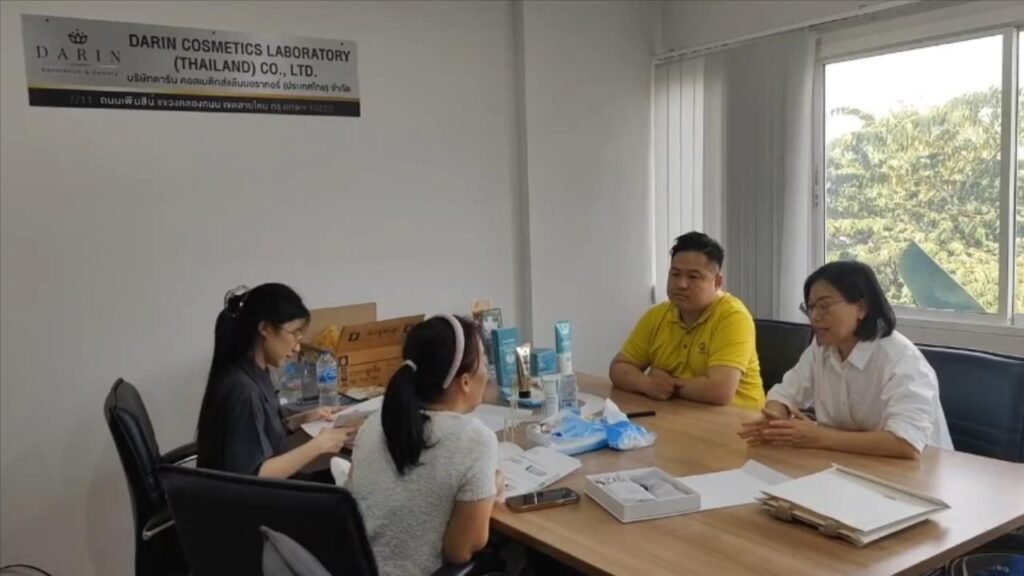
l Functional area division and product application
According to the demand of cosmetic production process, this project divides the clean room into the following core functional areas and realizes the environmental control objectives through customized products:
- Personnel decontamination areas
Changing room and buffer room: set up double changing rooms ( first/second changing), equipped with intelligent air shower room developed by OUDELONG.
Function: the blowing wind speed ≥ 25m/s, can remove more than 90% of the particles on the surface of the personnel; door frame sealing strip built-in pressure sensor, real-time monitoring of airtightness, to ensure that the differential pressure gradient ≥ 10Pa.
- Core production areas
Filling workshop (ISO 8): using our modular clean wall panels (color steel plate + antimicrobial coating) with silicone sealing of joints, air tightness up to EN 12114 standard.
Packaging workshop: the floor is epoxy self-leveling, with a slope of 1.5% to achieve fast drainage, certified by TIS 876-2557 anti-slip.
- Material management area
Raw Material Warehouse and Cargo Shower Channel: Installation of roller conveyor belt cargo shower room, equipped with HEPA filtration system, material passing time is shortened to 20 seconds/batch.
- Equipment support area
Air-conditioning plant room: Installation of our two-stage fresh air pre-treatment unit (primary filtration + surface cooling dehumidification), combined with a rotor dehumidifier to stabilize the dew point temperature below 12°C.
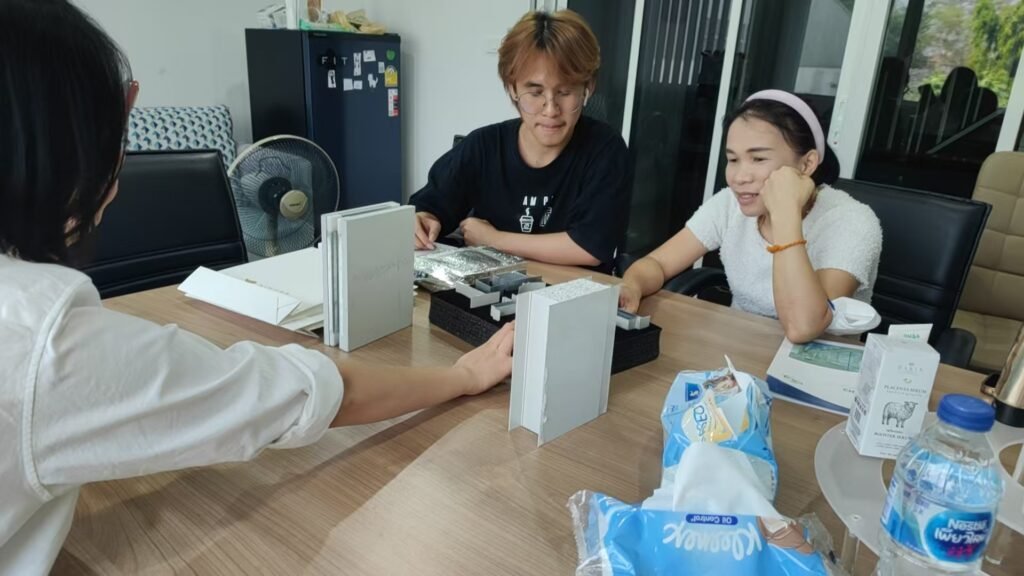
l Design Challenges and Solutions
Challenge 1: Maintaining Cleanliness in a Hot and Humid Climate
Problem: With 75% humidity in Bangkok during the summer, traditional wall panels are prone to mold and mildew, and epoxy floors are prone to condensation.
Solution:
Wallboard resin coating with nano zinc oxide particles passed ASTM G21 standard 1000 hours mold test;
Floor construction with humidity-sensitive coating, automatically activate the floor heating dehumidification system when the humidity is >65%.
Challenge 2: Human/logistics cross contamination control
Problem: The distance between the locker room and the filling plant is too long, and personnel movement tends to disrupt the differential pressure gradient.
Solution:
Optimize the design of the moving line, and compress the walking distance of changing room-air shower room-filling workshop to 15m;
Set up differential pressure self-adjusting dampers in the buffer zone, with the fluctuation range controlled within ±2Pa.
Challenge 3: Balancing equipment energy consumption with cleanliness
Problem: Conventional laminar air supply systems increase energy consumption by 40% in the tropics.
Solution:
The air conditioning system integrates a heat recovery device, which uses the energy of the exhaust air for the pre-cooling of the fresh air, and reduces the comprehensive energy consumption by 20%.
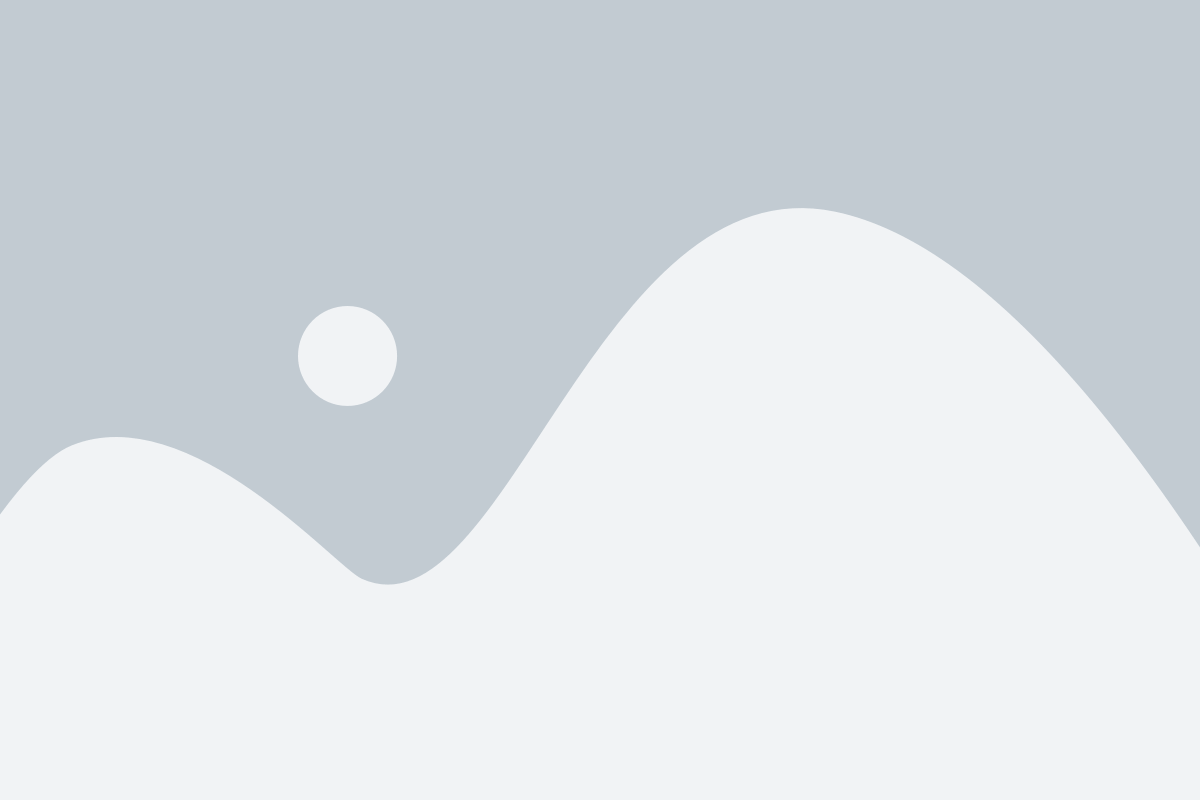
l Construction process management
- Segmented construction and quality control
The clean room is divided into filling area, packaging area and buffer area with three major modules for synchronized construction. The laser level is used to calibrate the verticality (error ≤1.5mm/m), and dust particle sampling is carried out in every 20 square meters area.
- Intelligent monitoring
Real-time monitoring of temperature, humidity and differential pressure data, and automatic trigger warning when deviation exceeds the limit.

l Industry Value and Future Expansion
This project provides a replicable technical template for cosmetic cleanrooms in the tropical region of Southeast Asia:
Standardized product library: Modular wall panels, intelligent air shower rooms and other components have formed a rapid adaptation program;
Asset-light mode: focusing on the “design-product-service” chain, complementary cooperation with general contractors, and reduction of customer investment risks.
l Conclusion
Under the extreme challenge of Bangkok’s hot and humid climate, we have realized efficient cleanroom engineering through material innovation, intelligent control and modular design. In the future, we will continue to deepen our focus on the special environmental needs of the tropics and provide more flexible and sustainable clean solutions for the global cosmetics industry.