Pinnacle Adhesive Electronics Cleanroom Engineering Practice
in Bangkok, Thailand
--Environmental control solutions for the production of high-precision electronic insulation materials.
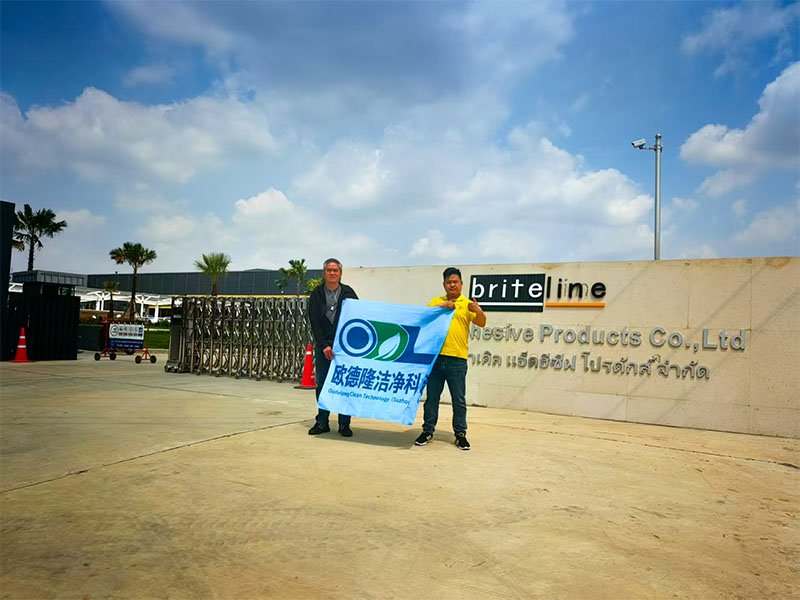
Client: Pinnacle Adhesive Products Co., Ltd
Industry: Fabric Mills, Textile Mills , Manufacturing, Electric insulating tapes and braids, except plastic
Address: 89 Ratchadaphisek Road 20th Floor, Room 2004-2007 (S-01), AIA Capital Center DIN DAENG, BANGKOK, 10400 Thailand
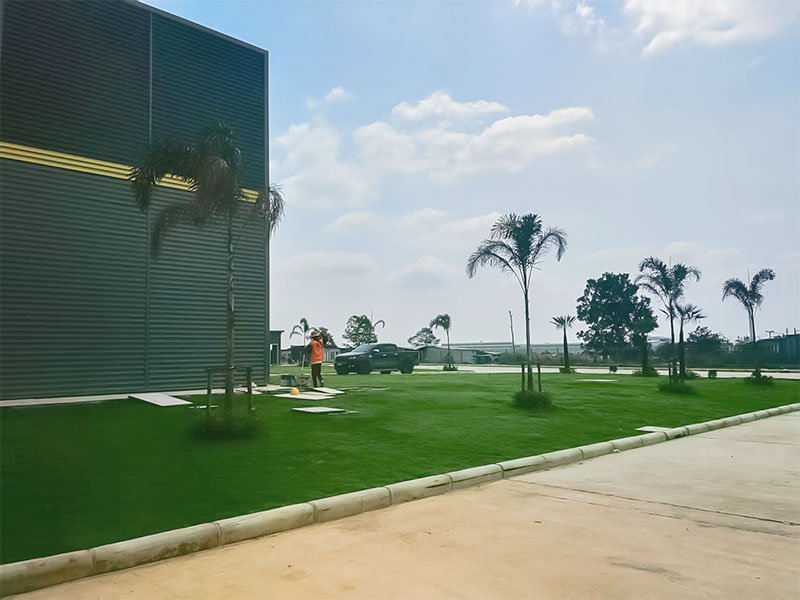
I. Project Background and Functional Area
Pinnacle Adhesive Products Co., Ltd specializes in the manufacturing of electronic insulating tapes and woven tapes, and its Bangkok plant is located at AIA Capital Center, Ratchadaphisek Road, in a clean room that meets ISO 14644-1 Class 7 (Class 10,000) standards.7 The core functional areas include:
- Raw material storage area:temperature and humidity control (20-25°C, humidity ≤ 40%), with moisture-proof epoxy resin floor and air-tight shelves.
- Coating workshop:core production area with the highest cleanliness requirements (≥0.5μm particles ≤352,000/m³), equipped with anti-static wall panels and laminar flow air supply system.
- Slitting and packaging area:anti-static design, installed with ionic air rods to eliminate material surface charge.
- Quality inspection laboratory:independent differential pressure control (+15Pa), equipped with HEPA filtered ultra-clean bench.
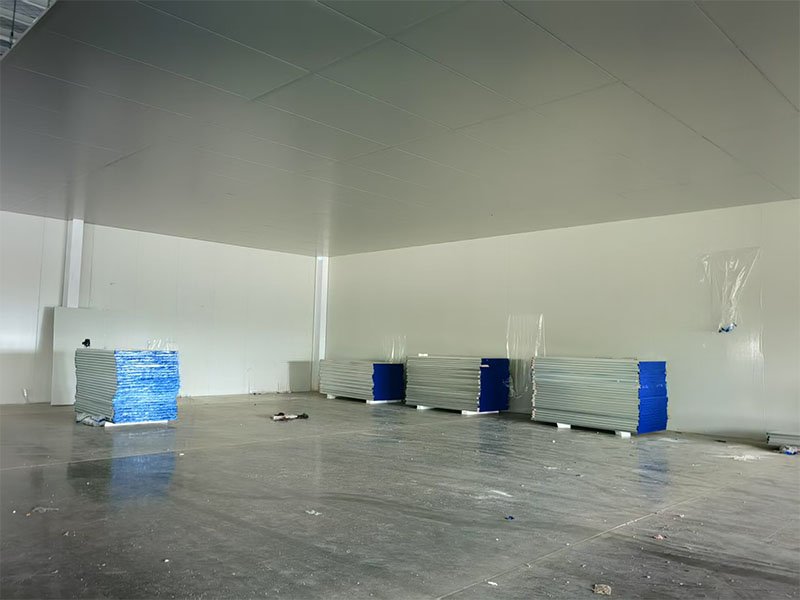
II. Core design challenges and innovative solutions
1.Dual challenges of hot and humid climates and static electricity control
- Challenge:75% humidity in Bangkok during the summer months can easily lead to moisture absorption in the insulation, while the coating process generates static electricity (surface resistance needs to be ≤1×10⁹Ω).
- Solution:
- Composite wall panel system : new material structure, surface resistance ≤1×10⁶Ω, anti-static certification through IEC 61340-5-1.
- Two-stage dehumidification system: rotor dehumidifier + refrigeration dehumidification combination, humidity control accuracy ±3%, energy consumption is 25% lower than traditional solutions.
2 Synergistic management of differential pressure in multiple regions
- Challenge:There was a risk of cross contamination of dust between the raw material area and the coating plant.
- Solution:
- Dynamic differential pressure control: VAV variable air volume valve is adopted to adjust the air supply in real time through the IOT sensor to maintain the gradient of coating workshop (+20Pa) > slitting area (+15Pa) > warehouse (+5Pa).
- Airlock chamber design: double-door interlocking airlock is installed at the material transfer port, with differential pressure fluctuation tolerance ≤2Pa.
Lorem ipsum dolor sit amet, consectetur adipiscing elit. Ut elit tellus, luctus nec ullamcorper mattis, pulvinar dapibus leo.
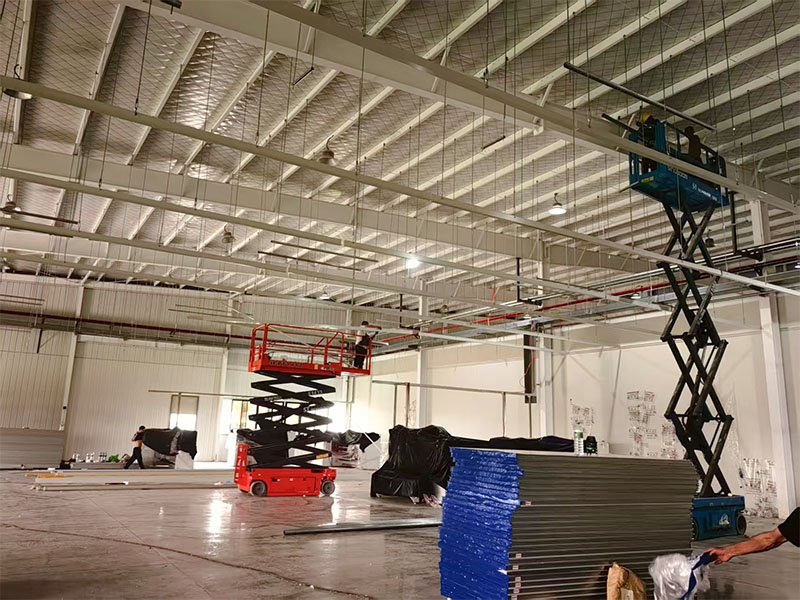
III. Key product applications and technical value
1.Anti-static modular wall panels
- Material innovation:wall panels sandwich add zinc oxide particles, static decay time <2 seconds, while inhibiting the growth of mold.
- Construction process:BIM technology is used to pre-buried pipelines, wall panel splicing joints are sealed with conductive silicone, and the difference in surface resistance is ≤5%.
2.Intelligent air shower and logistics system
- Personnel purification:air shower room equipped with high-speed air jets, blowing time of 12 seconds can remove 99.97% of 0.3μm particles.
- Material Transfer:Roller type goods shower channel with integrated static eliminator, surface voltage is reduced from ±15kV to within ±100V (IEC 61340 standard).
3.Energy-efficient air-conditioning system
- Heat recovery design:Exhaust air energy is used to preheat the fresh air, saving about 180,000 baht per year in electricity cost.
- Zoned temperature control:the coating workshop adopts independent constant temperature unit (±0.5°C) to avoid fluctuation of adhesive coating thickness.
IV. Conclusion
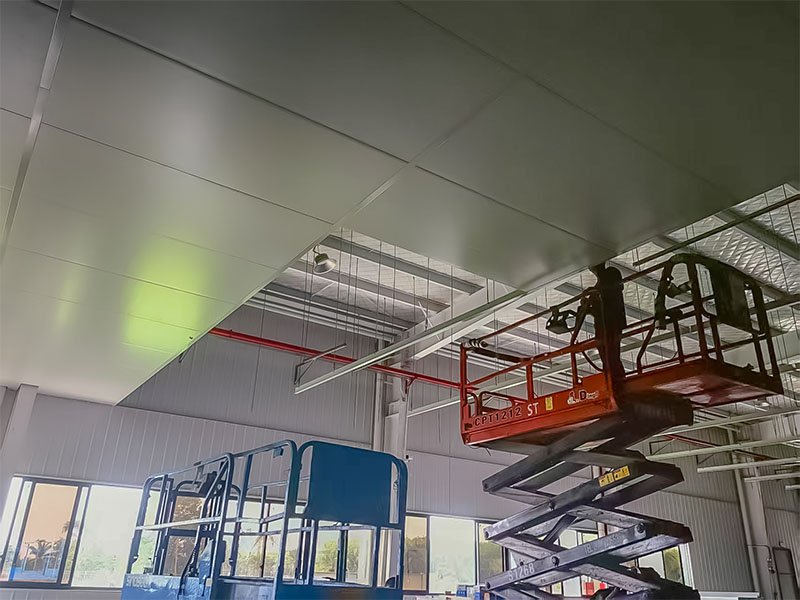
To meet the special needs of electronic insulating material production, we have achieved a double breakthrough in cleanroom performance and energy efficiency through material modification, dynamic environmental control and intelligent system integration. This project provides a replicable environmental control paradigm for the electronics manufacturing industry in Southeast Asia, and helps our customers enhance their competitiveness in high-end markets such as 5G materials and insulation components for new energy vehicles.
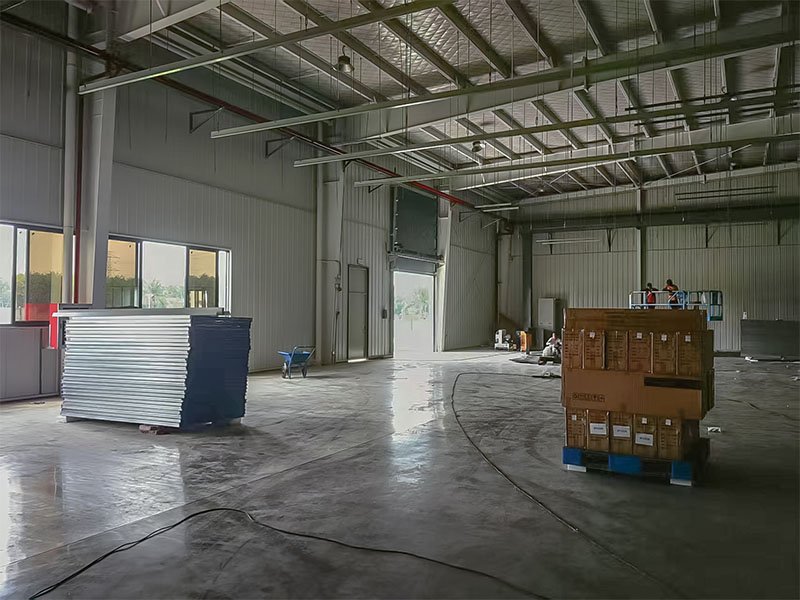